Trenchless Technology Used for Minot Lift Stations
Apex was recognized for Trenchless Technology use by the North American Society for Trenchless Technology (NASTT) by being selected to present at the 2016 No-Dig Show in Dallas, TX. The associated paper titled, “Utilizing Trenchless Technology for the Expansion of a Wastewater Collection System in a Booming North Dakota Oil City” was also recognized, as it was selected for publication in NASTT’s peer-reviewed journal.
The work acknowledged was the final section of a new 10-mile wastewater collector and three associated lift stations that the City of Minot selected Apex to design. This three-mile-long, 24-inch force main utilized multiple trenchless technologies. The new force main runs longitudinally underneath 55th Street, a valuable truck bypass around Minot for Bakken oil traffic, and crosses US Highway 2, which is the main route into the Bakken from Minot. Apex was able to complete the project with minimal disruption to traffic patterns on 55th Street and US Highway 2 while meeting all stakeholder needs and budget requirements by utilizing trenchless technologies.
Minot, North Dakota is located in the Bakken Oil Formation and has seen dramatic growth since the early to mid-2000’s. In order to prepare for future growth and relieve stress on the City’s existing collectors, Minot created the North Minot Sanitary Sewer Study in 2011 to evaluate the potential needs of the City. It was decided that the City would proactively install wastewater collection and three new lift stations to service the City’s rapid growth and relieve stress on existing wastewater collectors.
Apex conceived a wastewater force main system to parallel 55th Street for much of the project, while intersecting the road, railroad tracks, and US Highway 2, eventually finding its way to the City’s Wastewater Treatment Facility. Factors such as utilities, road and railroad crossings, and the available corridor had to be taken into consideration during design. To minimize disruptions, Apex opted for trenchless horizontal directional drilling (HDD) when crossing 55th Street and US Highway 2 as opposed to traditional open-cut installation. While HDD typically takes place 40-60 feet below the surface, Apex consulted with multiple HDD companies and determined a 30-foot installation depth would suffice. At this depth, only minor hydraulic fractures, or frac-outs, would occur. The railroad and perpendicular road crossings employed another trenchless technology in auger boring to complete the crossings without disruption to traffic and meet the stringent requirements required by the railroad.
Pipe material selection was imperative to the success of the project. Following hydraulic analysis, it was decided that a nominal 30-inch PVC pipe would be required to meet flow velocities while minimizing pump horsepower, reducing the overall cost of the project. The decision for the type of pipe came down to two options: fusible high-density polyethylene (HDPE) and fusible polyvinyl chloride pipe (FPVCP). Both options offered logical support for why it should be selected, although the FPVCP was ultimately chosen due to the larger inner diameter, strength, and cost-effectiveness. To prevent damage to existing infrastructure, FPVCP was used for the majority of the project.
Construction on the project began in the summer of 2014, with a stretch of sanitary sewer being installed south of US Highway 2. This allowed the pipe to be strung down 55th Street prior to pull back during the use of trenchless technologies. The drill rig was setup adjacent to the 55th street bridge, with no disruptions to traffic and no strain put on normal traffic flow within city limits. Largely because of the use of trenchless technologies, all parties involved viewed the project as a success.
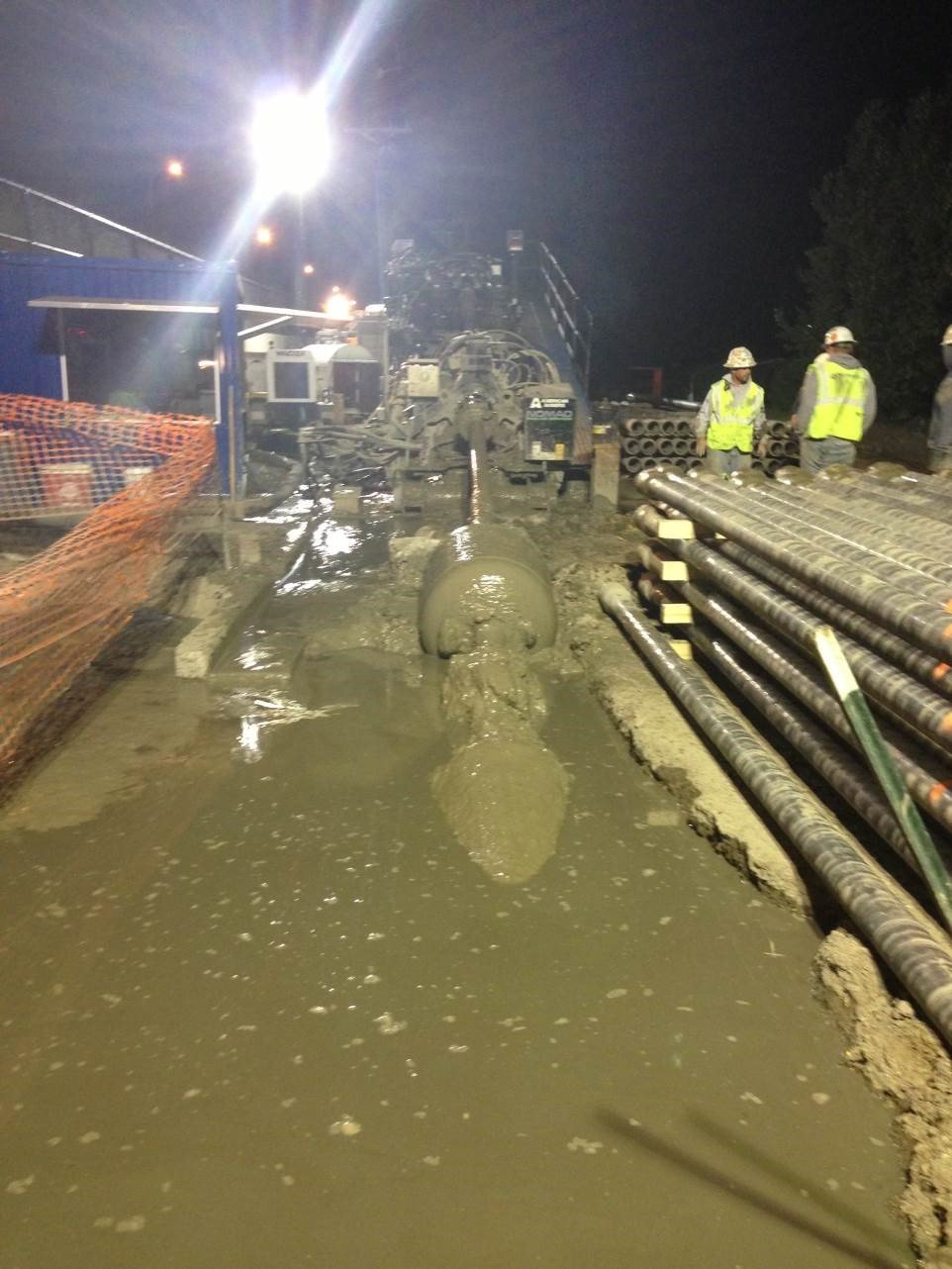